In warehouses, optimizations for more efficient and faster work are often welcome. This can be done by refining existing work processes or replacing used tools, but also by deploying modern robots if this is not already being done. Autonomous Mobile Robots (AMRs) are trying to set a standard in this area, by being better than the somewhat better-known Automated Guided Vehicles (AGVs). We visited Zebra Technologies to get some more insight into the warehouse worker’s handy little helper.
Not everyone will immediately see the match between Zebra Technologies and robots. After all, the company is known to many from scanners and mobile computers. However, the goal of all Zebra technology is to support front-line workers, including in the warehouse. To offer more in these environments than the software and equipment Zebra Technologies already had, it acquired Fetch Robotics in the summer of 2021. It thus added several AMRs to its product offering to further automate warehouses. This by letting robots take over tasks that employees don’t really want to do. That way, it gets the best out of employees, is the idea.
From AGVs to AMRs
Autonomous Mobile Robots are different from Automated Guided Vehicles. In many cases, the latter category of machines is already present in warehouses. AGVs, like AMRs, can be used to move goods. What an AGV does differently is that it follows a configured route for which it uses wiring, for example. This is the “guided” part of the machine. It allows the machine to follow only the configured route. If there are no obstacles, this obviously works fine.
AMRs, however, are smarter than AGVs. These robots have a map of the warehouse in which they operate. When instructed to deliver goods at a certain point, they determine the best route for themselves. Obstacle do not cause the robot to come to a complete stop to wait for the obstacle to be moved. They navigate around a moving or stationary object to still get to the end point. If necessary, they may take an entire detour between other racks to do so. The AMR will use allowable zones and no-go zones, though, when properly set up in advance.
Basically, this brings us to the fundamental difference between AGVs and AMR. Still, what is striking about the robots we see is how the employees in the Zebra warehouse handle the machines. They find it all pretty straightforward. When they want to use the AMR to move goods, they can easily give the instructions. Zebra Technologies will no doubt insist on using its own technology a lot and correctly in its own warehouse, but it does show that AMRs are robots that a large group of workers can handle.
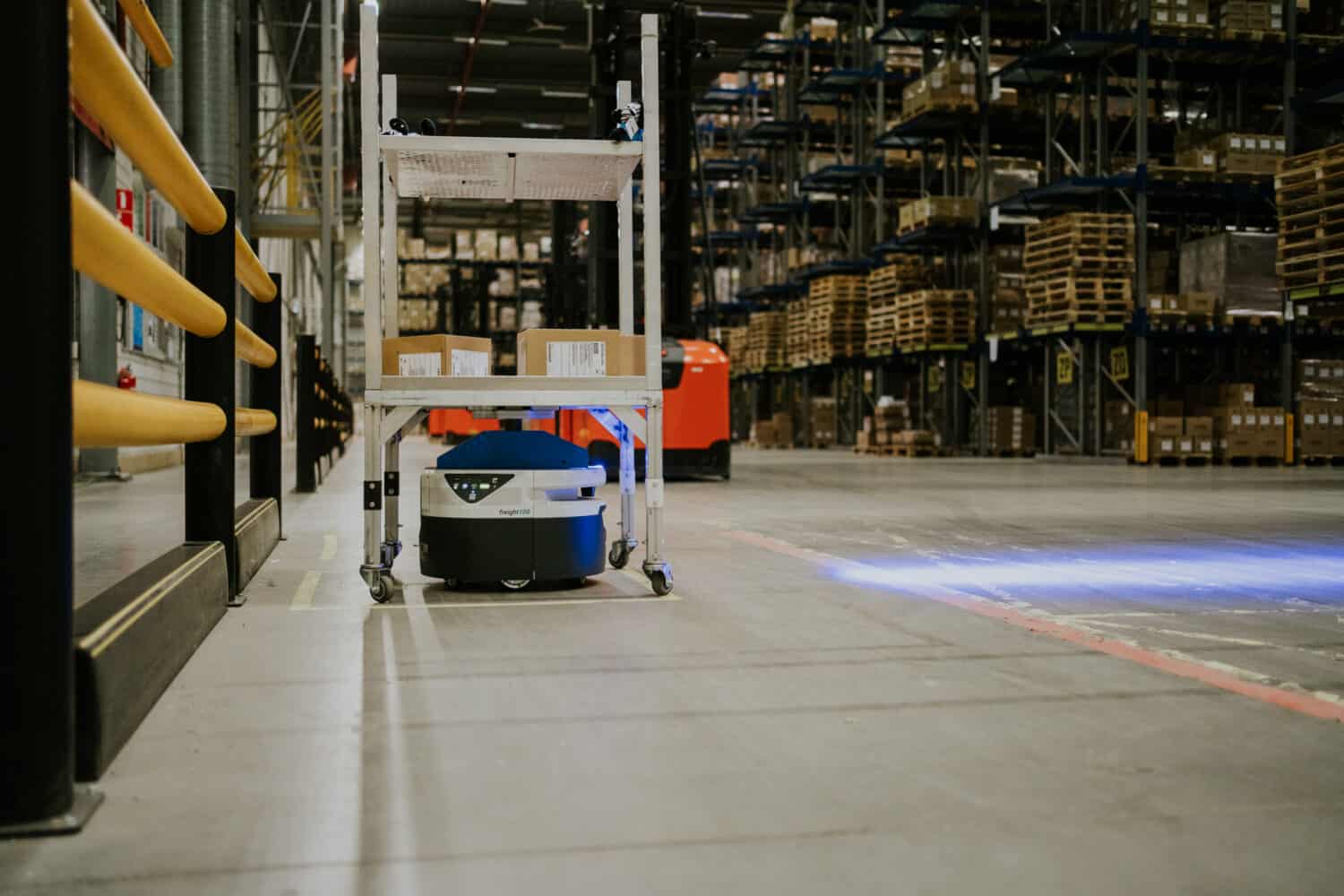
Making work more pleasant
According to Marcel Kars, VP of Robotics Automation at Zebra Technologies, AMRs in a warehouse can ultimately provide many benefits. He cites an example that an employee in a less automated warehouse walks 15 kilometers a day, sometimes for much of the time with heavy items. That can be physically demanding, as well as taking up a lot of time. If you can automate much of that away with robots, Zebra Technologies sees a happier employee emerging. The employee can focus more on primary tasks. Or the higher-value tasks, as Zebra Technologies describes them. Think of repairing and replacing broken packaging and products. People are simply still needed for such tasks. Right now, as far as we can see, there are no fully covering robots for such high-value tasks.
So what Zebra Technologies is trying to do with the acquired Fetch Robotics machines is take over work that robots can perform. According to Kars, that also removes some errors, as the robots perform repetitive work flawlessly. The theory is that workers are prone to errors in repetitive tasks. Eliminating those errors combined with saving time and allowing workers to perform more attractive tasks make the investment a no-brainer, in Kars’ view.
Setting up the environment incrementally
Kars points out that warehouses can feel free to roll out robots incrementally, getting a little more efficient each time. For example, they can start with a small robot with a roller conveyor for conveying tasks. Such a robot can be used for loading and unloading and help with rush orders. Ultimately, that can get companies excited and possibly encourage them to purchase other robots. For example, Zebra Technologies also has AMRs that can be used to move racks or very heavy pallets. The image below gives an idea of the different Fetch Robotics AMRs.
The above robots show the diverse use cases of AMRs. According to Zebra Technologies, you’re really going to see more efficiency down the line by making them part of your existing investments in ‘intelligent automation’. This is where the company sees an advantage by pairing with the somewhat more traditional Zebra tools. For example, handheld scanners and tablets provide visibility of inventory in the warehouse to simplify management. Linking AMRs to that information, and linking the information from AMRs to traditional Zebra tools, can create some additional visibility and achieve automation.
More efficient through AMRs
It should be clear that AMRs aim to be a handy aid to the warehouse worker. With current market conditions like a labor shortage and faltering supply chain, that extra help is a good investment as far as Zebra Technologies is concerned. But even when such problems disappear, AMRs can provide a desired efficiency boost. Fearing that they will completely automate warehouse work is not necessary, because high-value tasks will still require people. It is a combination of people and technology that Zebra Technologies says the world is really looking to for added efficiency.
Also read: Zebra provides visibility and mobility for on-demand economy